摘 要:以某中型車座椅橫梁為研究對象,從選材設計、結構設計和工藝設計等方面全面介紹了熱塑性復合材料座椅橫梁的輕量化設計方案及制造技術;并通過零部件的性能檢測和減重效果評價,驗證了產品符合使用性能與設計要求,可有效替代原鈑金結構,并在成本未顯著提升的同時實現減重32%,可有效降低整車油耗,對滿足國家油耗強制法規提供了有力支持。
引 言
在我國汽車產業飛速發展的同時,能源安全、節能減排已經成為汽車產業可持續發展所面臨的重要問題。國家出臺了一系列的政策法規,對汽車的能耗和排放指標均進行了嚴格的限制,而汽車輕量化正是解決上述問題,滿足政策及市場需求的重要手段。
碳纖維復合材料(Carbon Fiber Reinforced Polymer/Plastic,CFRP)以其優異的機械性能、抗疲勞性能以及遠低于金屬的密度條件,成為了汽車輕量化的首選材料。但是,目前90%以上的汽車用碳纖維復合材料均采用熱固性樹脂體系,這類材料存在回收困難、固化周期長等問題,對滿足《汽車有害物質和可回收利用率管理要求》將造成較大影響。為此,熱塑性碳纖維復合材料就成為解決這一問題的有效手段。
連續纖維增強熱塑性復合材料具有較好的機械性能,目前多通過模壓工藝實現成型,但是,受工藝特性限制,無法滿足一些特殊結構的成型要求。對于這類復雜結構,目前多采用注塑成型的方式,但使用的纖維長度僅3 mm左右,制品的機械性能較差,較難滿足車身結構件的使用要求。
如果將模壓工藝與注塑成型的方式結合起來,以連續纖維增強熱塑性復合材料為骨架,并通過注塑成型的方式實現復雜結構的成型,則可同時滿足汽車零部件對性能和結構的需要,進一步拓展熱塑性復合材料在汽車結構件上的應用。
為此,項目組依托“國家自然科學基金-中國汽車產業創新發展聯合基金”U1664250課題,以某中型車的座椅橫梁為研究對象,通過采用模壓-注塑混合成型工藝的形式,進行了全流程的設計開發,在降低零部件質量的同時,深入研究了模壓-注塑共性關鍵技術問題,為模壓-注塑混合成型工藝在整車上的批量應用積累了寶貴經驗。
1. 模壓-注塑座椅橫梁的選材設計
該中型車座椅橫梁由前座椅前橫梁、前座椅后橫梁、后座椅橫梁等構成,以前座椅后橫梁為例,該零部件如圖1所示,由橫梁本體、左側加強件和右側加強件3部分組成,其尺寸規格為589 mm×140 mm×110 mm。該零部件采用傳統鈑金結構,將3個獨立鈑金件焊接在一起,并通過螺接方式與座椅連接,是典型的車身梁類結構件,總體質量為1.85 kg。
圖一:某B級轎車前座椅后橫梁
模壓-注塑復合材料的材料主要涉及增強纖維和熱塑性樹脂的選擇。
對于模壓-注塑混合結構,為了確保模壓層與注塑層之間的界面性能,模壓區域和注塑區域宜選用相同的樹脂體系。而常用熱塑性樹脂中,POM、PEEK、PEKK等材料流動性差,很難滿足注塑成型過程中的充模要求,且材料成本過高,因此不宜考慮;而流動性較好的PP、PA6、PA66等材料中,綜合表1中對不同樹脂性能-成本的對比分析,PA6具有更優異的性價比,且性能可以滿足汽車零部件的應用要求,因此作為首選樹脂材料。
不同樹脂的性能-成本對比如表1所示。
注:表中數據均為添加30%玻纖后的復合材料數據
而對于增強纖維,目前常用的主要有碳纖維和玻璃纖維2類。其中,玻璃纖維價格較低、抗拉強度也較高,但拉伸模量相對較低;而碳纖維雖然強度和模量都非常高,但價格太高,目前還無法滿足汽車的成本控制要求。
從表2給出的不同纖維增強復合材料性能對比可以看到,玻纖增強尼龍6材料(PA6)的拉伸強度顯著高于原鈑金件使用的HC340/590DP鋼,但拉伸模量卻不足鋼材的1/3;在等剛度設計條件下,零部件厚度需增至原鈑金厚度的3倍以上,無法有效發揮出復合材料的輕量化效果。如部分使用碳纖維,則可有效彌補玻纖模量不足的缺陷,降低部件厚度,使零部件最大程度實現減重。
表2 不同材料性能對比
而玻纖增強尼龍6注塑料雖然強度和模量都較低,但可通過結構筋的形式提升零部件的整體剛度,且密度小、成本低,因此可以較大程度替換連續纖維增強尼龍材料,實現減重降本的目標。
因此,在滿足剛度條件的情況下,選擇玻璃纖維增強尼龍6為零部件材料主體,混雜部分碳纖維增強尼龍6材料改善零部件整體剛度,并通過短玻纖-尼龍6注塑筋進行局部剛度補強,完成了模壓-注塑座椅橫梁選材方案的制定,如圖2所示。
圖2 座椅橫梁選材方案
圖2所示的本體區域采用連續纖維增強PA6材料,連續纖維由碳纖維和玻璃纖維共同組成,并在滿足性能需求的基礎上盡可能多地提高玻璃纖維比例,以降低用材成本;圖2所示的加強筋區域采用非連續玻纖增強PA6的粒料,纖維體積含量為30%~50%。
2. 模壓-注塑座椅橫梁的選材設計
2.1 原始的座椅橫梁鈑金件由橫梁本體、左側加強件和右側加強件、2個焊接螺母及1個焊接加強板等6個部件組成,各部件之間通過焊接的方式連接在一起。改為模壓-注塑復合材料結構后,成功的將原有的6個部件簡化為1個零部件,并在注塑過程中將螺母預埋到零部件上。
集成結構如圖3所示:
圖3 座椅橫梁集成設計方案
從集成設計方案可以看到,橫梁的上部為模壓結構,起到主要載荷的承載作用,并與周邊零部件連接;橫梁的下部為注塑筋結構,主要對零部件的扭轉剛度進行補強。
2.2 變厚度設計
根據座椅橫梁受力需求及原鈑金件結構,對復合材料座椅橫梁進行了變厚度設計。
從圖3可以看到,座椅橫梁鈑金件的左右兩側,橫梁本體與加強件有較大區域的重疊結構,并通過焊接方式構成封閉截面,因此整體結構剛度更高,改為復合材料結構后需要增加鋪層厚度,以滿足性能需求;橫梁中間區域僅由橫梁本體構成,為單層鋼板結構,剛度較低,可以適當減少鋪層厚度,降低材料質量和成本。
變厚度的設計方案如圖4所示,其中左側和右側為加厚層,本體壁厚為4.05 mm,共23層;中段為減薄層,本體壁厚為3.55 mm,共21層;注塑區域壁厚為2 mm。
通過進行結構優化設計,復合材料座椅橫梁的總體質量為1.23 kg,與原鈑金件的1.82 kg相比,實現減重30%以上。
圖4 座椅橫梁變厚度設計方案
2.3 連接結構設計
替換為復合材料后,座椅橫梁無法與地板及周邊零部件進行焊接,因此改為膠粘的方式,涂膠區域如圖5所示。
圖5 座椅橫梁膠粘區域設計方案
通過膠粘的方式,既可以滿足零部件的結構連接性能需求,還可以對復合材料與鋼材的界面起到隔離作用,降低CFRP與鋼接觸部分可能產生的電化學腐蝕風險。同時,膠層還可以與復合材料協同作用,進一步降低震動對乘員艙的影響,降低車內噪音。
3. 模壓-注塑座椅橫梁的工藝制造
復合材料座椅橫梁采用模壓+注塑的混合成型工藝,工藝流程如圖6所示。
具體步驟如下:a.根據鋪層設計方案,將連續纖維增強PA6預浸料進行鋪層,將鋪層好的復合材料板材進行預熱,待樹脂軟化后移入模壓模具,壓制成座椅橫梁預成型件;b.取出模壓預成型件,進行裁邊、打孔、預埋等處理,并通過紅外加熱等形式對預成型件進行二次預熱;c.在較高溫度條件下,將預熱后的模壓預成型件快速移入注塑模具,進行注塑加筋處理;d.開啟注塑模具,取出最終的零部件。
通過二次預熱,可有效提升注塑過程中,注塑筋與模壓件的界面結合性能。但預熱后的模壓件移動較為困難,且移動時間過長將會導致表面溫度降低,難以達到預期目標,因此需要通過機械手臂自動完成,以提高工藝的一致性和穩定性。生產熱塑性復合材料座椅橫梁使用的模具如圖7a和圖7b所示。
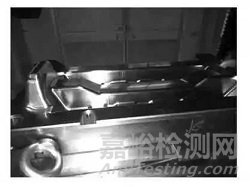
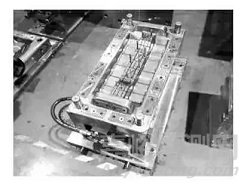
(a)模壓模具 (b)注塑模具
圖7 座椅橫梁模壓-注塑模具
通過模壓、預熱、注塑等工藝,完成了零部件的試制,制得的碳/玻混雜纖維復合材料座椅橫梁樣件如圖8所示。
圖8 座椅橫梁樣件
4. 模壓-注塑復合材料座椅橫梁樣件的試驗驗證
根據座椅橫梁在車身結構中的主要貢獻,制定了部件-臺架-整車級性能驗證計劃,開展了包含零部件外觀檢測、零部件尺寸公差檢測、零部件力學性能檢測、臺架試驗和整車搭載檢測等多項測試,具體如下。模壓-注塑復合材料座椅橫梁力學性能檢測結果見表3。
a.表面質量符合設計要求,表面光滑、平整,纖維紋路整齊,無針孔、裂紋、漆點以及砂紙印等明顯的外觀缺陷;
b.外形尺寸符合設計要求,通過裝車檢測和三坐標檢測,產品的裝配尺寸公差符合設計要求;
c.對座椅橫梁的強度、剛度、安裝點性能等各項力學性能進行檢測,其檢測的結果如表3所示;
表3 模壓-注塑復合材料座椅橫梁力學性能檢測結果
d.用模壓-注塑復合材料座椅橫梁替換替換設計車型原有的鈑金結構,通過座椅安全臺架試驗,座椅安裝點未發生拔脫現象;
e.搭載模壓-注塑復合材料座椅橫梁進行設計車型的道路試驗,在車速為120 km/h時,未出現共振抖動等不良現象。
5. 模壓-注塑復合材料座椅橫梁的輕量化效果評價
與原鈑金橫梁相比,模壓-注塑復合材料座椅橫梁的質量及其減重效果如表4所示。
表4 模壓-注塑復合材料座椅橫梁質量及其減重效果
結語
通過對模壓-注塑復合材料座椅橫梁的設計開發、試制和驗證,掌握了模壓-注塑混合成型工藝的選材、結構設計和工藝制造特點,并得出如下結論。a.采用模壓-注塑混合成型工藝,可成功制造具有復雜加筋結構的復合材料零部件,并同時滿足汽車結構件對機械性能的需求;b.在模壓-注塑混合成型過程中,模壓和注塑部分宜選擇相同的樹脂體系,并在注塑前對模壓預成型件進行預熱,以提高模壓-注塑界面的結合性能;c.通過合理的選材和結構設計,模壓-注塑復合材料座椅橫梁的力學性能顯著優于原鈑金結構,可有效改善整車性能;d.與原鈑金件相比,模壓-注塑復合材料座椅橫梁的減重率達到32%,減重效果明顯;e.模壓-注塑座椅橫梁選用熱塑性復合材料體系,易回收,結構性能優異,輕量化效果顯著,且可通過多材料混合應用的方式降低零部件成本,是碳纖維及其復合材料在汽車領域應用的重要發展方向之一。
